RAPID PROTOTYPE MOLDING (RPM)
Fast Prototypes to Test Form, Fit and Function
Reduce your design risk with RPM, a prototyping solution that delivers functional injection molded prototypes in a fraction of the time and cost of a fully-tooled solution.
RPM is a process in which we 3D print a negative cavity of the part using a dissolvable resin, then inject HX5 into that 3D printed mold, resulting in a prototype that is:
Fast
Inexpensive
High-Quality
To learn more about how RPM can reduce your design risk, including how it compares to traditional 3D printed prototypes, complete the form to get things started.
Want to get a high-performance prototype in a matter of days?
Let's chat!
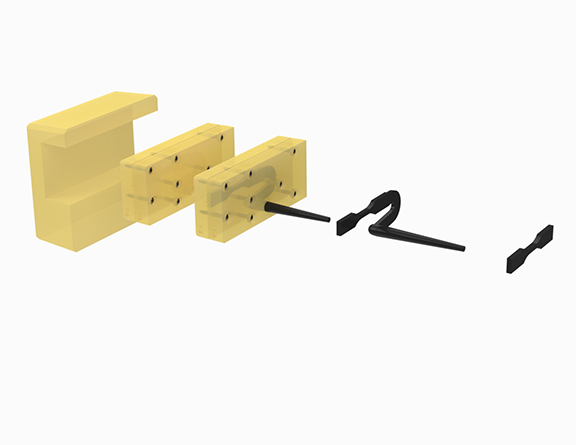
BENEFITS OF RPM:
RPM provides unparalleled design flexibility, allowing you to create intricate, customized parts with a high degree of dimensional accuracy. Using RPM, you can create prototypes with:
- High mechanical integrity for prototype parts (near full final part strength and much stronger than 3D printed parts)
- Advanced material resins not available for 3D printing
These prototypes closely resemble the final product, allowing for testing and verification of their performance. Contact us to learn how our RPM capabilities could apply to your project.
A key advantage of RPM is that it provides extensive testing opportunities. This process enables the evaluation of physical prototypes before initiating mass production with steel tooling. During the testing phase, our engineers:
- Ensure alignment to desired performance specifications
- Identify weaknesses or issues early in the design process
- Validate mechanical performance has been characterized by third party testing
Each part is optimized for best performance through iterative refinement, ensuring that the final result is production ready. Contact us to learn more about third-party testing opportunities.
Unlike steel tooling, RPM offers the convenience of swift iterations and modifications during development. Designers can thoroughly experiment with, test, and refine designs before progressing to production. This iterative validation process provides several key advantages:
- Quick and inexpensive technique for testing various gating configurations and designs
- Minimizes the risks associated with mass production
- Optimizes the production process, streamlines operations, and scales up efficiently
RPM is an optimal solution for manufacturing prototypes with the shortest lead time and lowest cost compared to other manufacturing techniques.
COMPARATIVE ANALYSIS: PROTOTYPING AND TOOLING WITH RPM
Prototyping and tooling are pivotal aspects of the manufacturing process. Explore through the tabs below the distinctions between RPM and 3D printing and traditional steel tooling:
Prototyping: RPM vs. 3D Printing
ATTRIBUTE | RPM PROTOTYPE | 3D PRINTED PROTOTYPE |
Lead Time | 2-4 weeks | A few days |
Strength | Higher* | Moderate |
Material Options | Real-world, production-level IM materials | Proprietary 3D printing materials |
DFM | Design applicable to production-level IM | Design restricted to 3D printed methods |
*RPM prototypes are stronger because unlike 3D printing, fiber alignment can be achieved with injection molding.
Tooling: RPM vs. Steel
ATTRIBUTE | RPM 3D PRINTED TOOL | PRODUCTION LEVEL STEEL TOOL |
Cost | Low, hundreds to a few thousand dollars | High, tens to hundreds of thousands of dollars |
Lead Time | 2-4 weeks | 6-16 weeks |
Configuration Flexibility | Multiple configurations possible | One configuration per tool |
Surface Finish/Textures | One finish | Multiple textures available |
Repeatability | Low, typically one part per tool | High, thousands of parts per tool |
Dimensional Accuracy | Typically 0.025" | Typically 0.008"-0.010" |
Part Size | Limited to size of 3D printer | Limited to size of injection molding press |
CASE STUDY
We compared projects similar in part count, size and complexity to determine the differences in tooling time and cost between RPM and traditional steel tooling to achieve validation test parts.